Triboconditioning®
The mechanochemical surface treatment method Triboconditioning® has been developed and patented by Tribonex. The treatment can be implemented as a superfinishing or mass finishing operation and can be carried out using standard machines. The result is a plateau structured surface with a changed surface chemistry that reduces friction and the wear of the component.
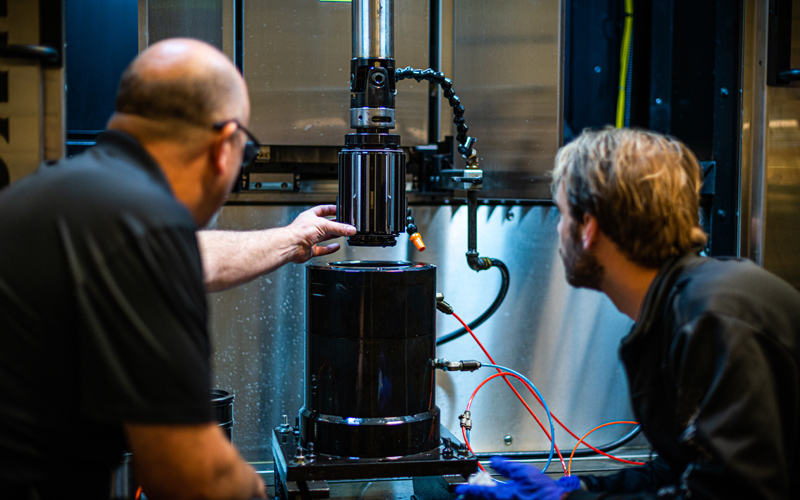
The Triboconditioning® features
How it is done
The Triboconditioning® process combines mechanical burnishing with tribochemical deposition of a friction and wear-reducing compound onto the component surface. Tools are used to work the surface, pressing in component asperities and creating a plateau surface roughness profile. The plastic deformation of the surface peaks releases energy which makes a special process fluid to react with the surface in the tool contact. A low friction and anti-wear tribofilm is thus formed on the component surface, well integrated and chemically bound to the surface.
Key to the process are the special reactive fluids used, that both protect the component during the machining, avoiding surface damage and scoring from the tool interaction, as well as changing the surface chemistry, which works as a low friction running in layer adding long lasting benefits.
A premier strength of the Triboconditioning® process is that it can be carried out using standard machines and finishing equipment, which makes the process very cost efficient in series production. Operator training and process operation is also simplified. Implementation is carried out using either standard CNC-lathes, VMCs or honing machines, suitable for parts with a round shape, such as outer diameters of shafts and inner diameters of cylinders. This process is called Triboconditioning® RS. Components with a more complex geometry such as gears, splines and pistons can be treated using Triboconditioning® CG which uses standard mass finishing processing platforms to create the mechano-chemical surface treatments.
Traditionally finished surface
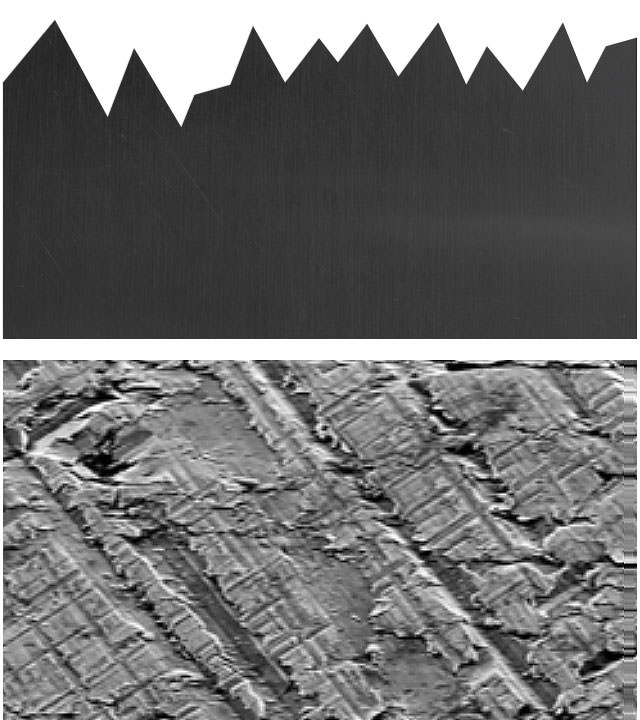
Triboconditioning® finished surface
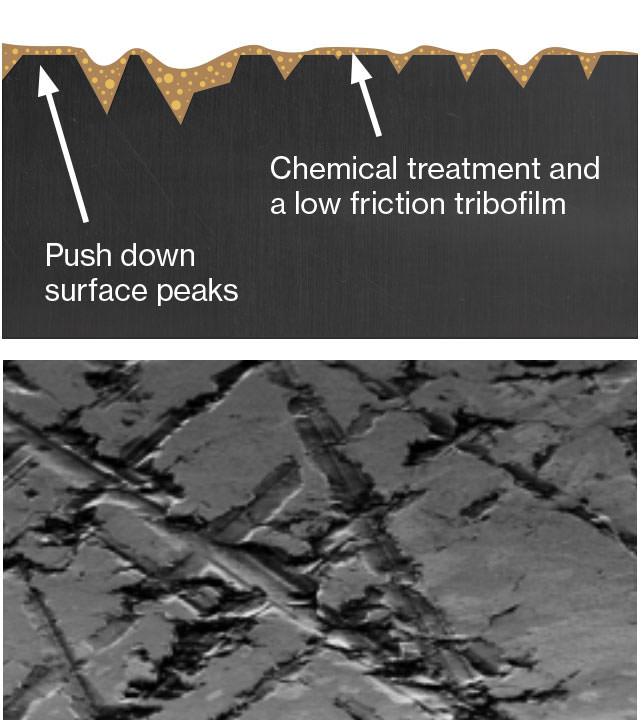
Effect
The Triboconditioning® technology greatly improves the tribological performance of the finished component in terms of wear-resistance and lowered boundary friction. The mechanical and chemical surface properties also increase the lubricant film strength, which makes it ideal for deployment in combination with modern energy-saving lubricants. As compressive stresses are introduced in the surface through the Triboconditioning® treatment an increased surface toughness and resistance to micro-pitting is also achieved.
The treatment results in:
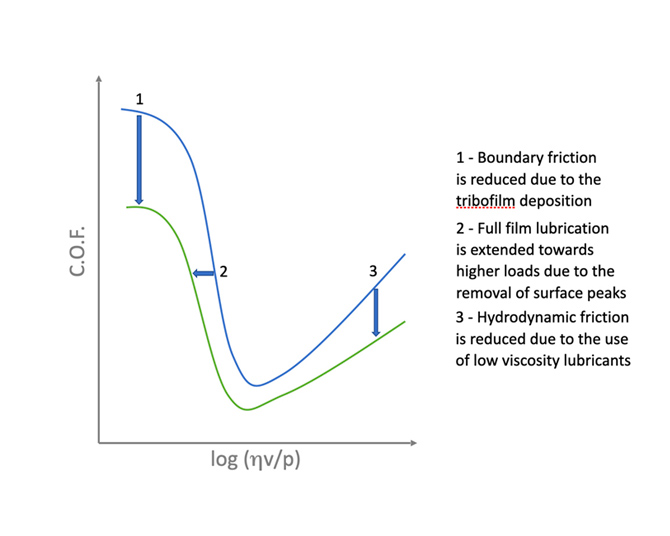
Triboconditioned® parts demonstrate less running-in wear during early life and preserve better surface integrity over the entire service life when compared to regular components.
Triboconditioned® parts demonstrate less running-in wear during early life and preserve better surface integrity over the entire service life when compared to regular components.
Application areas
The Triboconditioning® treatment is suitable for any machined parts that are made of steel, cast-iron and similar ferrous alloys.
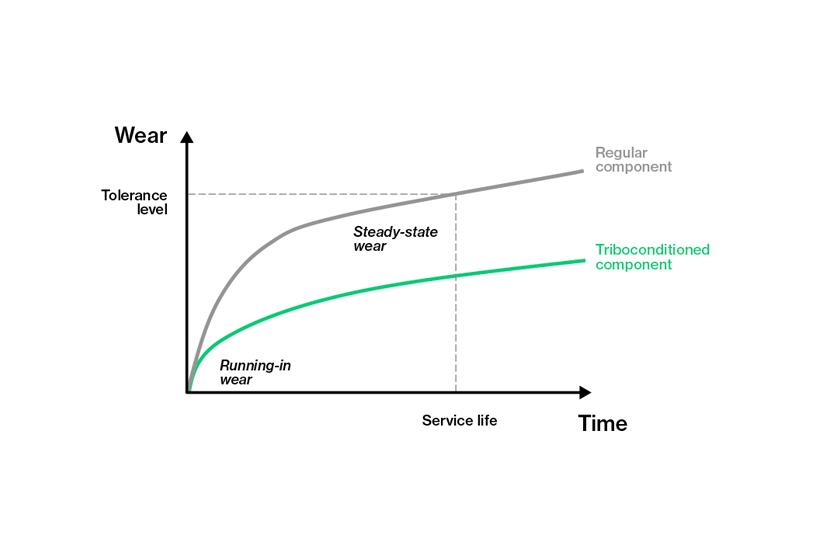
Application areas
Drivetrain components
Powertrain components
Industrial components
Triboconditioning® CG
How it is done
The treatment is implemented using mass finishing machine platforms. Tooling, processing parameters and reactive process fluids are selected based on component size, shape and application demands. As the process is flexible, components of variable and complex shape can be treated. As the Triboconditioning® CG process can significantly improve the surface finish, it can be either applied as an additional final finishing operation or as a process exchanging existing finishing steps, which can lower added on-cost.
The process is offered on a supply basis from Tribonex, from Tribonex’s select treatment partners or through direct implementation at our customers’ production plants through licensing. To support implementation, Tribonex has established relationships with leading suppliers of machines and tooling.
Effect
Triboconditioning® CG brings performance benefits in terms of increased component durability and efficiency. The Triboconditioning® CG treatment toughens the surface through introduction of compressive surface stress as well as the formation of an anti-wear tribo-chemistry in the surface. This improves system running in and brings significant protection against wear as well as reduced friction losses in a lubricated contact.
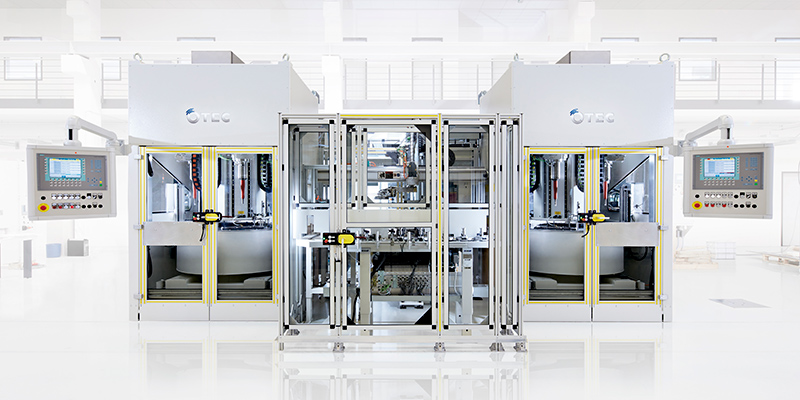
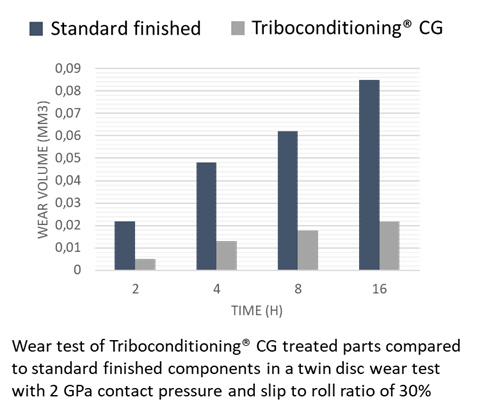
Triboconditioning® RS
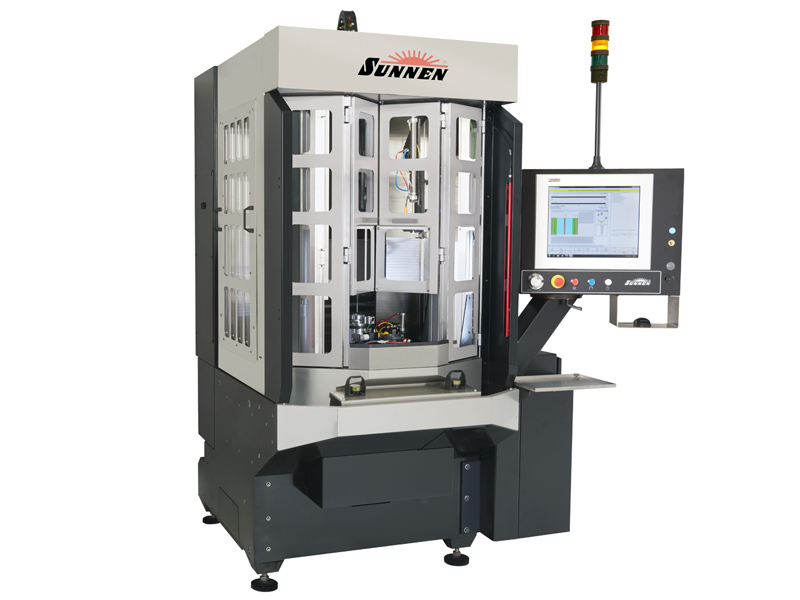
How it is done
The treatment is implemented using standard CNC-lathes, VMCs or honing machines, where a fixed tool is pressed against the component surface under high load in a sliding contact. The process is well suited for components of round shape (RS), where tool loads can be controlled over the whole surface. The process can exchange existing finishing processes such as superfinishing for improved performance.
The process is offered on a supply basis from Tribonex or through direct implementation at our customers’ production plants through licensing. To support implementation, Tribonex has established relationships with leading suppliers of machines and tooling such as Sunnen and Diahon.
Effect
Triboconditioning® RS brings performance benefits especially for components in conformal contact in a lubricated environment, where optimized plateau surface profile together with the low friction anti-wear tribofilm gives long term improvements when it comes to friction and wear.
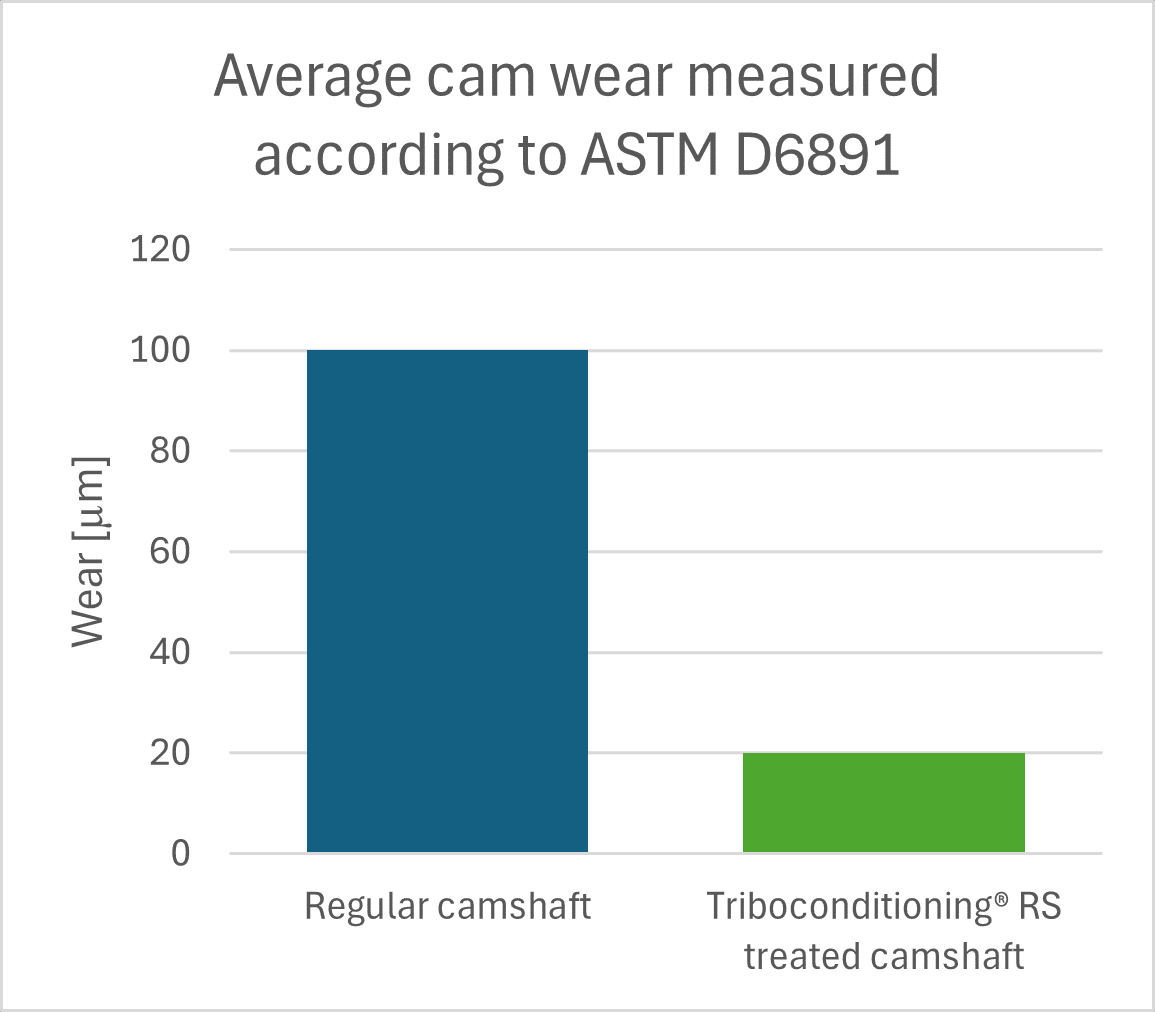