Industry implementation Case 1
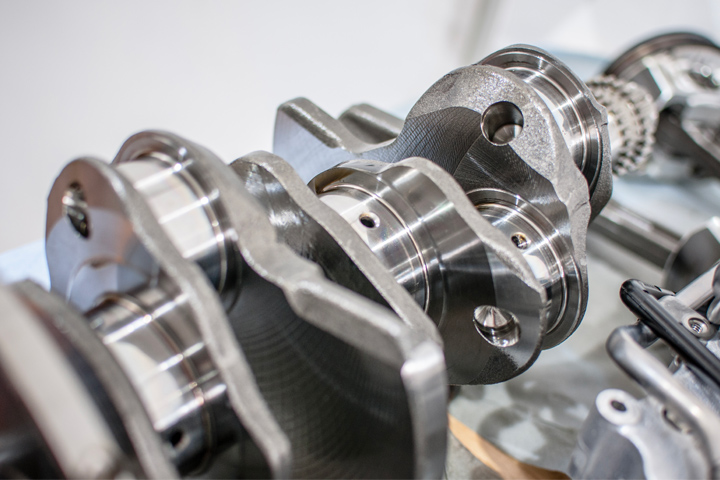
The challenge
Excessive bearing wear due to insufficient lubrication
Connecting rod bearing and crankshaft main bearing systems in an engine are supposed to operate in full film lubrication regime over the engine lifetime. However, deployment of low viscosity oils in combination with high loads in modern engines increase the operational window where full film operation is not achieved and therefore requires bearings that combine fatigue and wear resistance with the ability to combat dirt and slight misalignment.
If the engine bearings or crankshaft journals become worn, oil pressure will drop and the engine may start to burn oil. Generally, bearing wear specifically occur immediately after a cold start, before the normal oil pressure builds up.
A leading car manufacturer experienced excessive crankshaft main bearing wear in a high-performance engine, where modern low viscosity oils have been combined with the latest engine designs resulting in high compression rates and loads. The resulting bearing stress has translated into excessive bearing shell wear, compromising engine life.
Tribonex’s Solution
By applying Triboconditioning® RS treatment to crankshaft journals, an improved lubricant film strength and system resilience to crankshaft misalignment and oil contamination can be achieved. Incorporating an optimized surface profile together with the low-friction and anti-wear Triboconditioning® RS tribo-film help achieve an optimized system running in, minimized bearing wear and maintained long term performance.
The car manufacturer struggled to achieve a reasonable crank bearing life and turned to Tribonex for remedy. Close collaboration with assessment of initial surface profiles and achieved improved load bearing capability through journal treatment, evaluated in rig and fired engine conditions, resulted in an optimized crank bearing treatment that proved an 80% reduction in bearing wear and maintained performance over the whole engine life.
80% lowered bearing wear achieving target engine life
Improved start-stop efficiency
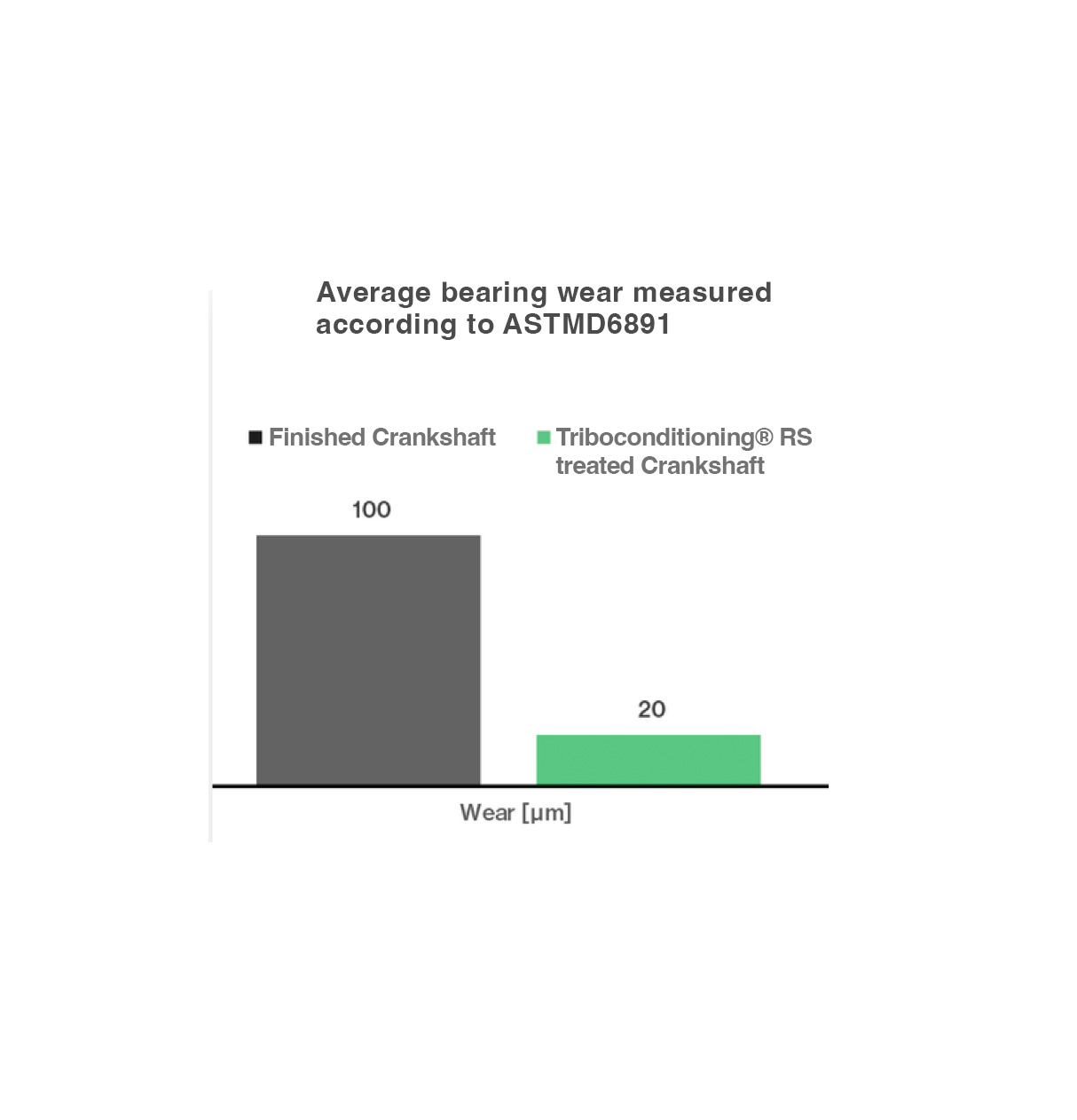
Industry implementation Case 2

The challenge
Reach 30,000 rpm for an e-axle
Overheating of transmission gears due to starved lubrication and excessive friction
Gear teeth wear and component failure
In order to make electromobility affordable, the trend in development of drives for EV’s is increasingly moving to e-axles. Electric motors, power electronics and transmission together form a compact unit that is integrated into the front or rear axle of the vehicle to save space. A compact drive module can then be integrated into a variety of different vehicle types without major design changes. The elimination of components and connecting cables, as well as simplified cooling, saves costs compared to the conventional distributed design.
In the development of a high-speed e-axle for electric vehicles, a world leading powertrain technology provider set-up an ambitions target; to achieve an e-axle design that would allow up to 30,000 revolutions per minute for the e-motors and a top speed of 240 km/h, when implemented in a Tesla model 3 car.
These targets exposed the transmission to extreme loads as well as starved lubrication. Too extreme for a conventional transmission, which was shown in tests where excessive friction and overheating resulted using conventionally finished transmission gears. An optimized gear finishing solution was therefore sought to improve gear tribology under these heavily stressed conditions.
Tribonex’s Solution
Through a close dialog with the customer, the Tribonex’s specialists recommended the Triboconditioning® CG treatment of the gear teeth for the high-speed e-axis. The Triboconditioning® CG treatment was applied to the gears on both the input and the output shaft using a standard mass finishing treatment platform together with Tribonex’s reactive process fluids. The resulting surfaces incorporated an improved negatively skewed surface profile, formation of a low-friction anti-wear tribofilm in the surface and increased surface compressive stress. All achieved through one integrated process step.
With the new solution, the transmission was proven to withstand the full drive cycles also at the demanding 30,000 rpm operation speed. Thus, the Triboconditioning® treatment enabled a significant increase in power and efficiency, increasing the EV’s performance range at a relatively low added cost.
Improved gear teeth durability and lowered friction
Allowing transmission operation at 30,000 rpm
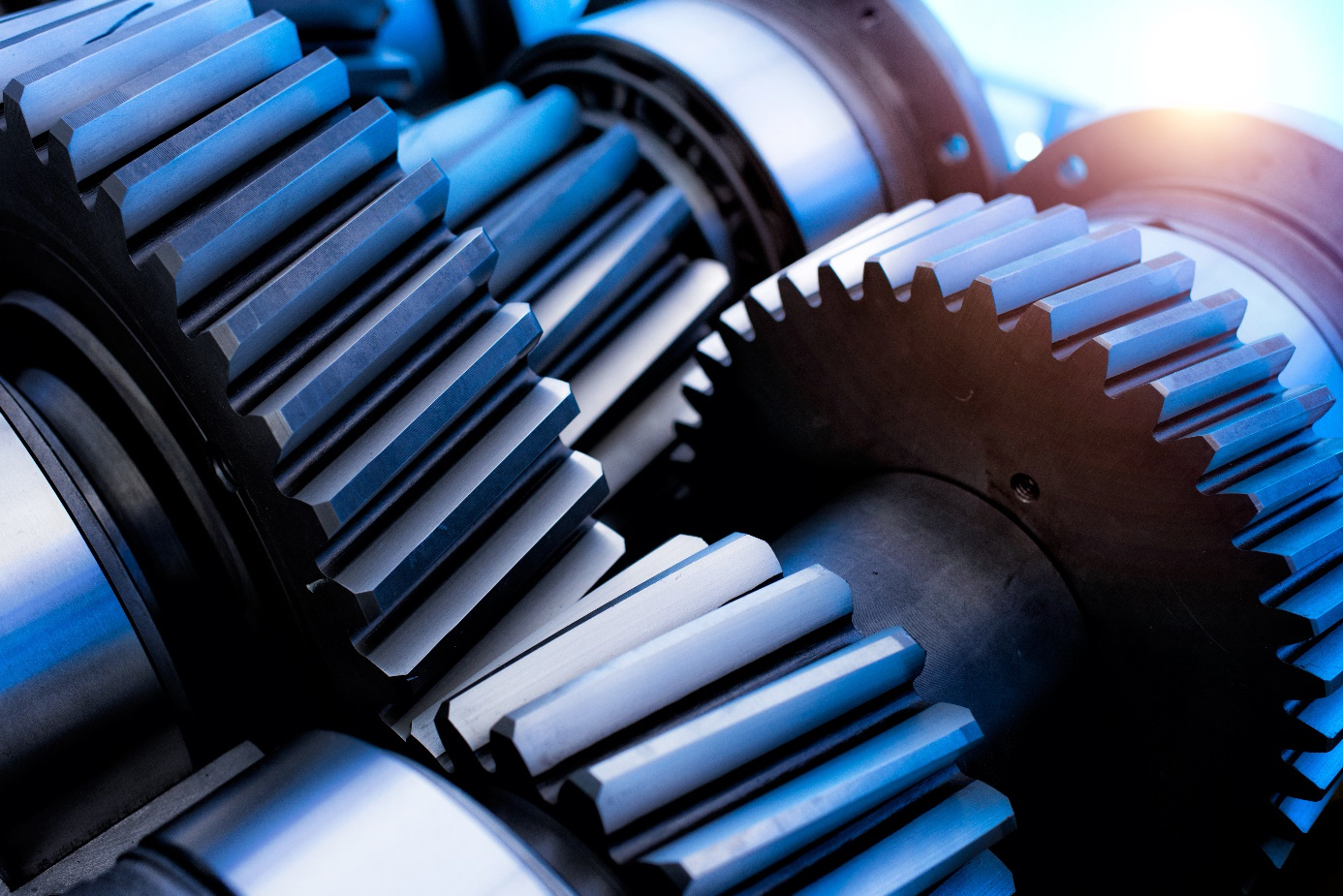
Industry implementation Case 3
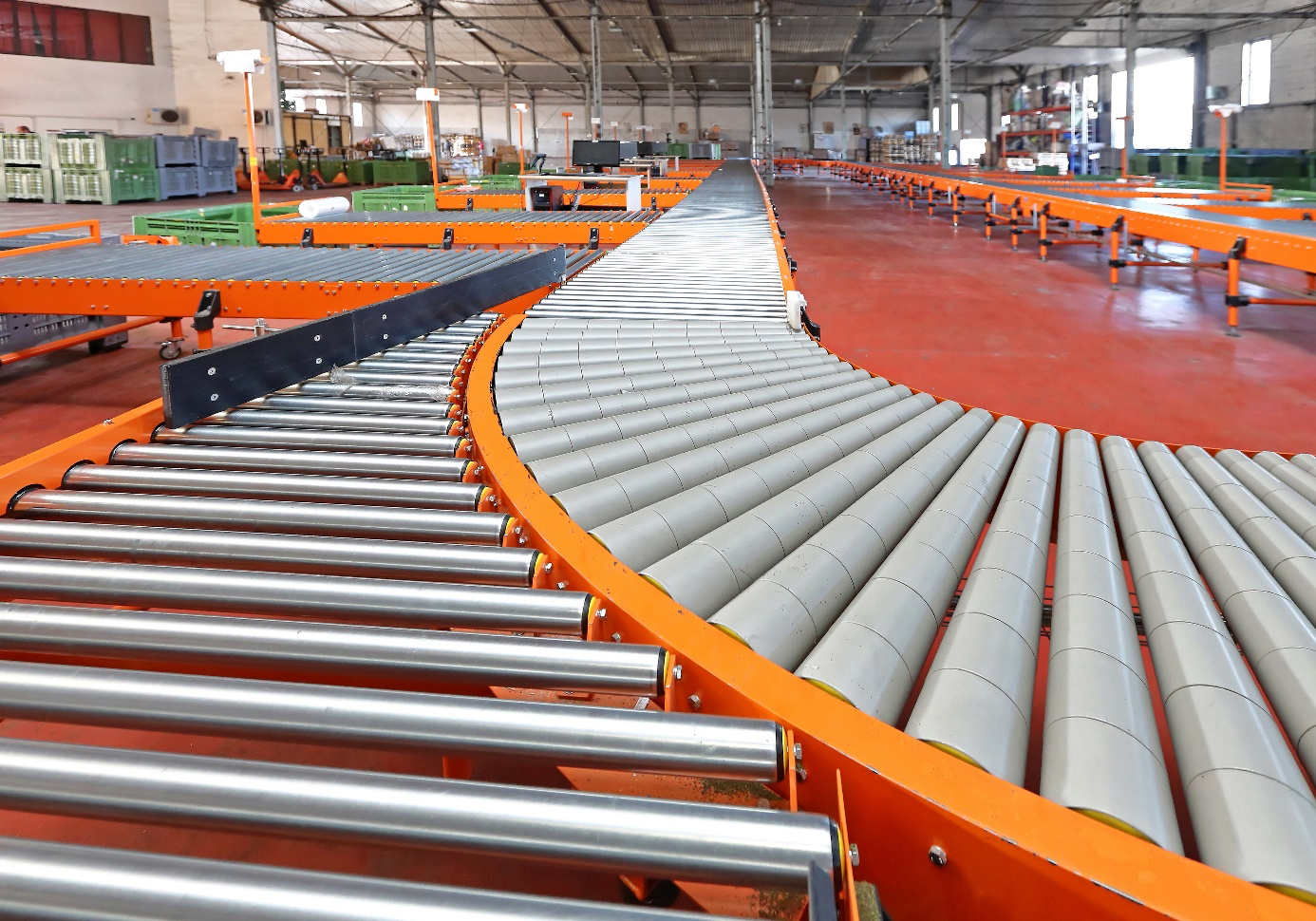
The challenge
Too high friction in conveyor system resulting in transport jams
Existing polymer type coating has too high wear rate and thus insufficient service life
Conveyor guide rails are a critical component in many automated systems. Inadequate rail design may result in jamming, damages and expensive downtimes. Guide rails are often made of stainless steel for corrosion resistance. Unfortunately, stainless steel is not a tribologically optimal material and has a sufficiently high friction against other materials. Therefore, low friction inserts or coatings are usually used. Polymer-bonded coatings are easy to apply, but they may fail to provide adequate service life due to rapid wear of the polymer.
Tribonex’s Solution
Tricolit® GO polymer-bonded coating developed by Tribonex in cooperation with Chalmers Institute of Technology uses graphene fortification for enhancing the abrasion resistance of the polymer material. Graphene sheets act as an armor leading to a significant increase in the coating service life. Tricolit® GO is a water-borne one-component coating system with zero VOC emissions and very low environmental footprint. The coating is applied by spraying, followed by thermal curing at 250C.
Coating of key segments of conveyor system lowered the friction and resolved transport jams
Up to ten times increased service life as compared to benchmarked polymer coating system
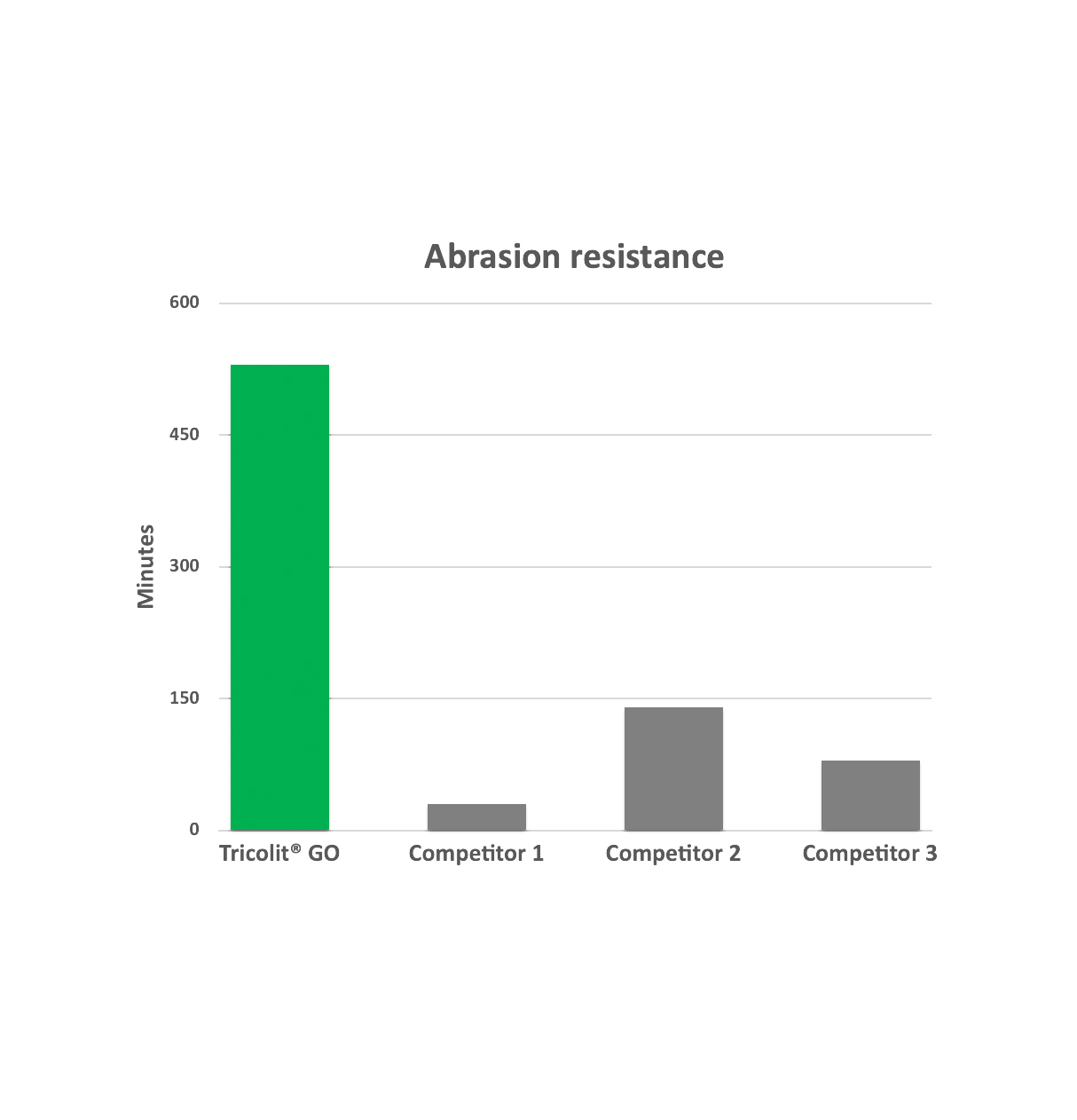